LABORATORY MANAGEMENT COACHING (FAST)
The purpose of the Laboratory Management coaching is to support scientific institutions to have access to functioning advanced scientific equipment. The strategy is unique and has proven successful. The programme addresses:
- Selection.
- Laboratory physical requirements.
- Transportation.
- Installation.
- Calibration.
- Training.
- Operation.
- Maintenance.
- Servicing.
- Use.
- Decommissioning.
The service is offered as support packages:
1. Equipment procurement and delivery.
2. Equipment management.
3. Construction of laboratories.
4. Operational & Financial plan development.
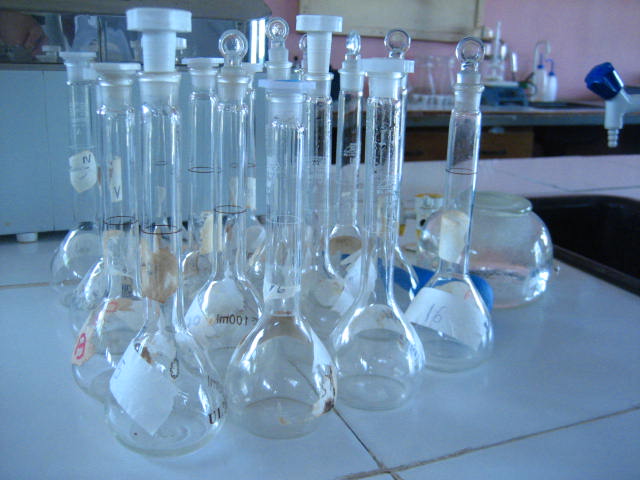
1. Equipment procurement and delivery
1. Identifying the theme of the Institution
The scientific institution identifies research topics with potential that would be strengthened if supported by advanced scientific equipment. The research topics shall be scientific disciplines that are core to the mission and objectives of the scientific institution as well as key research areas suitable for strengthening or building research capacity. A list of publications related to the selected scientific projects proposed is compiled, including papers published in international regional or national peer-reviewed journals. Also, the departments to be involved are identified. The institution submits the compilation to HR&S in Sweden.
2. Proposed items to be procured
The scientific institution compiles a proposal of the pieces of advanced scientific equipment to be procured together with accessories and consumables required for two years. The scientific institution also compiles training, services, maintenance, required for two years as well as the physical infrastructure improvements that may be required. The compilation and the expected cost are submitted to HR&S Sweden.
Now, the resource persons to be linked to the proposed new pieces of equipment are identified. It can be expected that the proper management of new equipment shall require the attention of truly dedicated, trained and well-equiped technicians. The technicians must also be given the authority to take action and to be able to run a smooth laboratory.
3. Stakeholder pre-procurement meeting
Joint meetings are arranged between i) the scientific institution management, researchers, technologists, and technicians, ii) HR&S staff and represenatives, iii) HR&S independent equipment expert adviser, and iv) the potential Agreed Suppliers. In the meeting, the proposed list of items is reviewed taking into consideration the research projects it shall be used for and the laboratory that shall host it. At these meetings, the researchers present the research projects for which the equipment is required. Thereafter the experts recommend revisions in the proposal, if needed. The experts may even propose appropriate manufacturers and suppliers. The discussiona are facilitated by HR&S staff.
4. Inspection of the laboratory facilities
The laboratory facilities intended for the new equipment are inspected by the potential suppliers and the HR&S independent equipment expert adviser, and succinct recommendations on physical infrastructure, work safety, and environmental protection are compiled. The inspections also include existing instruments at the laboratory facility that are either broken down or are simply not functioning, and which would benefit from being repaired. The discussiona are facilitated by HR&S staff.
5. Transportation, delivery, and installation preparations
The modalities for transportation, travel insurance, custom, delivery procedures, installation, installation training, service, and maintenance are discussed with the supplier and agreed on between the Institution and the potential Agreed Supplier. Options are presented in the operational plan guidelines. The discussiona are facilitated by HR&S staff.
6. Operational and Financial plans
The scientific institutions develops a firm HR&S Operational and Financial plans (O&F plans) including the advice provided by the experts.
The plans will among other things, guide the buyer on how much can be spent on the actual procurement and how much must be set aside for related products and services, taking into account the generation of funds to cover the running costs.
Tender
With these steps, the HR&S proposal is up for tender according to the local regulations. The offer contains the producs and services agreed on above combined with the HR&S coaching. The price may or may not be discounted. The price includes the cost for the HR&S coaching.
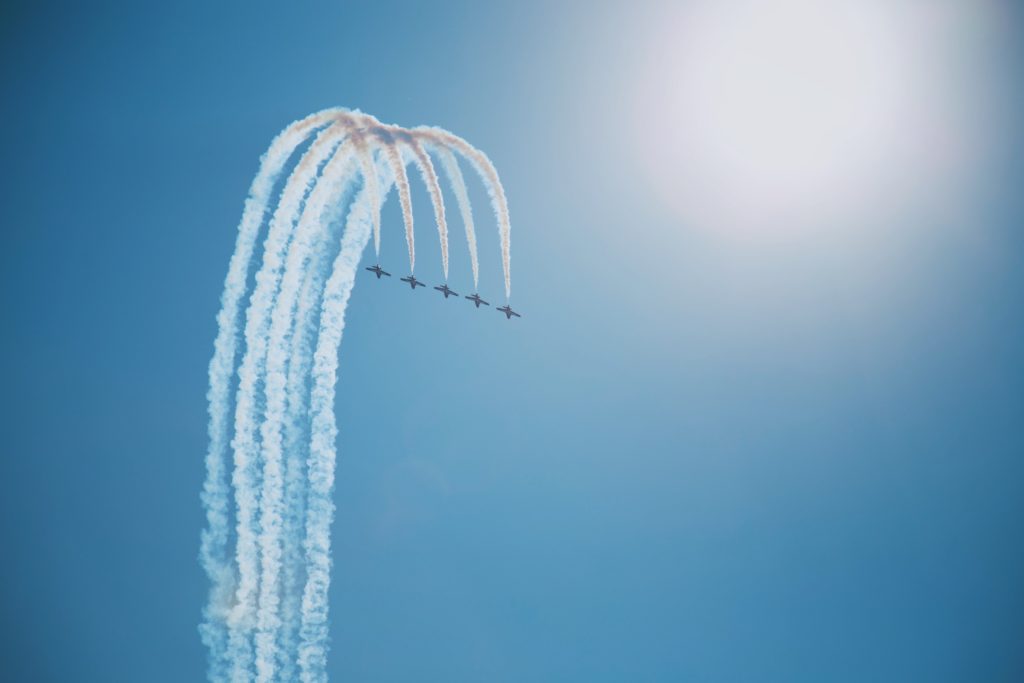
7. Laboratory inspection
The laboratories are inspected by the supplier and the order is not placed until the laboratories have been properly prepared to receive the equipment.
8. Placing order
The order is placed by the buyer and paid directly by the buyer to the vendor. A percentage of the equipment cost is paid when placing the order and the rest after the delivery and the checking that all items have been received according to the agreement.
9. Transportation
The items are transported and delivered within two months, unless otherwise agreed between the buyer and the vendor when placing the order. The vendor takes full responsibility for the transportation and custom clearence, and charges around 12,5 % of the procurement cost for the service.
10. Delivery
The scientific institution arranges firm procedures for how to receive the items. The items will be delivered by a transportation firm and the scientific institution discusses the time for delivery directly with the transportation firm, and at that time scientific institution have staff available to receive the items and directly transfer them to the storage rooms. The packing list provided by both the manufacturer and the supplier is compared with the items received. The items are documented with a camera. Any abnormality is reported to HR&S, the scientific institution management, the manufaturer and the supplier within 24 hours. If items are missing or damaged and it is not reported within 24 hours, then the responsibility to replace the items will be with the scientific institution.
11. Storage
The items are stored according to the specifications. Nothing is un-packed. This is again the responsibility of the scientific institution, and if not addressed properly, the scientific institution will have to replace mistreated items.
12. Installation and quality assurance
As soon as all items have been received and all facilities have been prepared, the supplier is called upon for installation and quality assurance. It is the scientific institution’s responsibility to ensure that the facilities are appropriately prepared and all items required for quality installation is available. The supplier will arrive to the scientific institution within one week, unless otherwise agreed with the buyer.
13. Installation training
Installation training shall be performed by the supplier according to the agreement, no later than two weeks after installation, unless otherwise agreed with the buyer. It is the responsability of the scientific institution to ensure that the expected trainees attend the installation training.
2. Equipment management
1. Operational and Financial plans
The previously developed Operational and Financial plans are reviewed annually by all stakeholders together. Constraints are indentified and solved and each item is followed-up on in actual practice.
2. Trainings
A package of trainings is agreed on. The trainees are compiled with names, positions, academic degree’s, responsibilities and experiences. All trainees do a test prior to developing the training package to ensure that the right level of training is choosen, not too simple and not too qualified. Trainings are provided at two levels, basic and advanced, and address; maintenance, service, general operation, advanced applications and quality assurance. The trainings can be arranged on-site, at national training centers or abroad and be provided by the manufacturers, the suppliers, equipment experts and trained trainers. The trainees receive certificates after having passed training exams.
3. Service by the supplier
The service contract can be negotiated to get large volume discount. Warranty is considered. Thereafter the service is managed according to the service contract between the buyer and supplier.
4. Exchange between laboratories
A pool of technicians with the appropriate training to do service and maintenance is developed as well as a pool of trained technician trainers. Exchange of knowledge and service among technicians and stakeholders is facilitated, this may include providing internet access. Visits are coordinated for technicians and researchers to stay at other laboratories to learn, through internship. Mutual exchange programs are facilitated e.g. to sending sample between members and receiving the results. Linkages with private sector laboratories are facilitated

5. Target partner meetings
Programme stakeholders meet bi-annually. All operational issues are discussed and all challenges addressed. Such meetings are necessary to address issues related to logistics; such as transportation, customs clearance, delivery, infrastructure preparations, installations, training, operations, service and maintenance. Other topics of the meetings can be:
• Arrange regular on-site meetings to screen existing equipment, assist researchers and technicians in getting the latest developments and techniques, offer maintenance and repair, and discuss other equipment related issue.
• Invite suppliers to the meetings for interaction and strengthening of peer networks of clients and users.
• Develop a charter with clear responsibilities between the universities and the suppliers on who does what in order to have the equipment operational.
• Inform suppliers of the potential marketing benefits if they manage to meet the actual needs of the Programme.
6. Equipment performance assessment
Equipment performance monitoring and evaluations are performed in real-time. The scientific institution is in charge of collecting monitoring data and HR&S supports with compiling, analysing and storing.
7. Outcome evaluation planning
Outcome evaluation planning is performed in real-time to evaluate if the support enabled the stakeholders to manage the new pieces of equipment in actual practice.
3. Construction of laboratories
Expert recommendations are offered in order to have laboratories prepared to receive the instruments.
Expert recommendations are offered regarding:
- The construction of buildings including general electricity, gas, and water installations.
- Specific electricity solutions, including generators and solar panels.
- Laboratory Internet Management System (LIMS) and general laboratory internet solutions.
- The design of laboratories including the efficient flow of samples through the laboratory system.
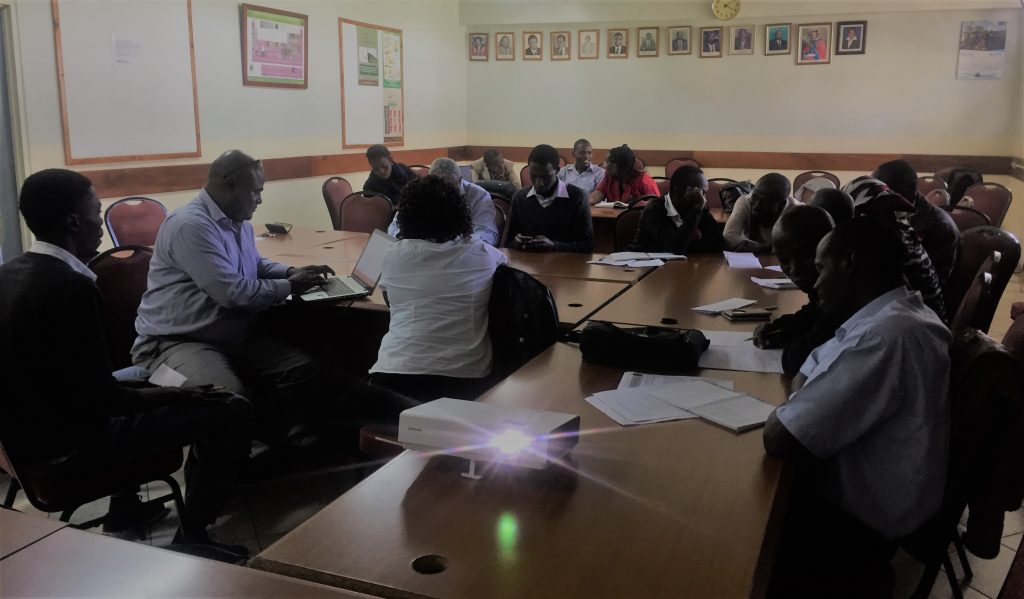
4. Operational and Financial plans
The Operational and Financial plans (O&F plans) are necessary and complementary procedures. The O&F plans offers the scientific institutions to reflect over how to prepare prior to procuring new equipment and how to manage the equipment after the procurement. The scientific institutions are themselves responsible for the development and implementation of the Operational and Financial plans (O&F plan). The plans should be annually reviewed and adjusted in relation to lessons learned. HR&S also offers stand-alone training and coaching on the O&F plans.
1. Training
Training on the Operational plan and Financial plan concept.
2. Coaching
Coaching on the development of O&F plans.
Operational plan
The Operational plan Guidelines has been developed to support scientific institutions with the procurement and use of advanced scientific equipment. The intention is that an operation plan shall be developed prior to procuring a new piece of advanced equipment. Thus each piece of equipment shall benefit from its own operational plan. The plan shall be filled in jointly by the institutional management, the researchers and the technologists technicians together. A separate document is generated for each piece of equipment.
Financial plan
Certain activities compiled in the operational plan, obviously come with cost implications, moreover the HR&S laboratory management programme is based on the principle of sustainable economy. Thus the operational costs for starting up a new piece of equipment necessarily have to be covered by an investment capital, but after about two years the equipment is expected to cover its own running costs as well as, whenever possible, generate a profit which can strengthen the laboratory or the research in general. A Financial plan Guideline has thus been developed to be complementary to theOperational plan Guideline document. The purpose with the financial plan is to prepare a strategy for the Institution to cover all the expenses that come with the running, maintenance and servicing of new or repaired piece of equipment. The financial plan compiles estimated costs as well as sources of funding. The cost recovery plan shows how costs related to procured or repaired equipment can be covered, and proposes options of funding sources.
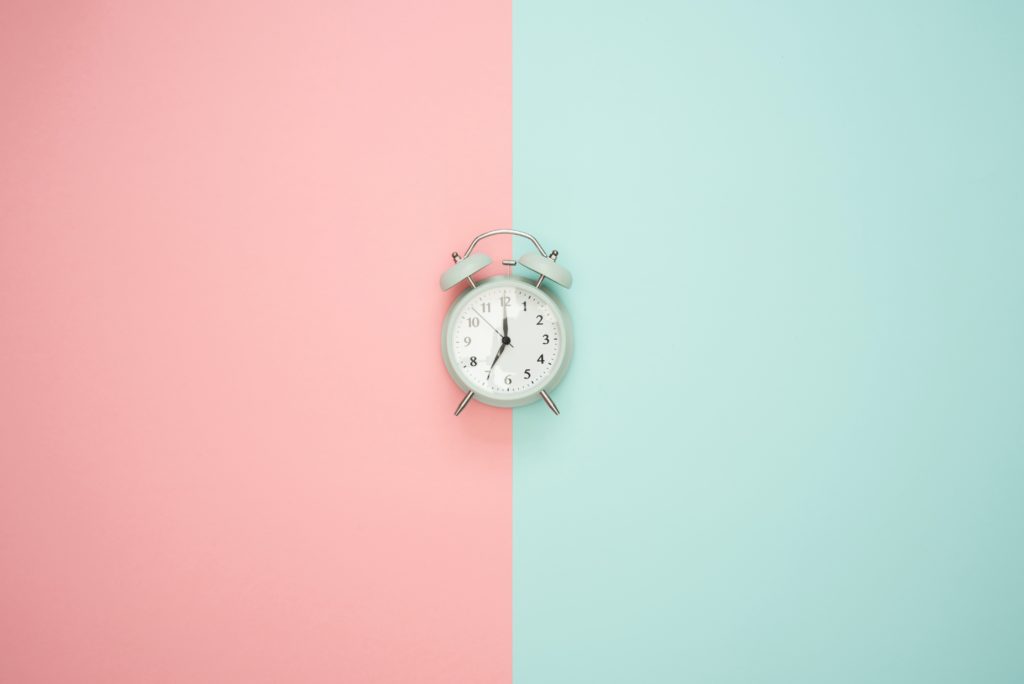
3. Evaluation planning
Each program builds on the Real-time Outcome Planning and Evaluation tool (ROPE) which measures whether the support provided by HR&S enabled the partner to be successful. It is the ambitions of the Partners which is the core of all programmes. ROPE provides; i) a strategy for designing programmes based on the needs and the knowledge of the Partners, ii) means to overcome the challenges identified by the Partners, iii) a sustainable economy, and iv) institutional capacity.
Acknowledgement
The Laboratory management coaching programme has been developed by Assoc. Prof. Cecilia ÖMAN.
She is grateful for the support provided by friends, colleagues and partners all over the world, especially Prof. Karniyus Gamaniel, Dr. Sune Eriksson, Dr. Amah Klutsé, Prof. Charles Aworh and Prof. Ado Dan-Issa. The five scientific institutions in Nigeria Amadu Bello University, Bayero University, University of Ibadan, University of Port Harcourt, and NIPRID, and two in Madagascar, Antananarivo University and IMRA, who were part of the pilot study are especially appreciated for having stretching beyond expectations to make the project successful. NIPRID is acknowledged for hosting the FAST Scientists Association of Nigeria. The FAST program builds on the output from the PRISM pilot project which was financially supported by the MacArthur Foundation in USA and managed by the International Foundation for Science (IFS) in Sweden.
References
Öman, C. and Lidholm J. (Eds) (2002) International Workshop on Purchasing, Servicing and Maintenance of Scientific Equipment in Western Africa, 5-9 November, Buea, Cameroon International Foundation for Science (IFS), Stockholm, Sweden. https://www.ircwash.org/sites/default/files/Oman-2002-Purchasing.pdf
Öman, C. B., K. S. Gamaniel, et al. (2006) Properly functioning scientific equipment in developing countries. Anal Chem 78(15): 5273-6.
Öman, B. C., Edward, R., Gamaniel, K.S., Klutsé, A., Eriksson, S., Hovmöller, H., Feresu, S., Gurib-Fakim, A. (2008) Procurement, Installation, Service and Maintenance Commitments for Scientific Equipment in Developing Countries – PRISM, Inventory of the current status of equipment and scientific infrastructure at selected universities in Africa and specification of what additional resources would be instrumental in strengthening scientific capacity. International Foundation for Science, Stockholm, Sweden.
Related documents
FAST Operational plan Guidelines.
FAST Financial plan Guidelines.